3-D Printed Ribcage Promotes Sternocostal Reconstruction
By HospiMedica International staff writers
Posted on 22 Sep 2015
A new study describes how a custom-made three-dimensional (3-D) titanium-printed prosthesis was used to reconstruct a chest wall.Posted on 22 Sep 2015
The procedure performed by surgeons at Salamanca University Hospital (Spain) was undertaken in a 54-year-old Spanish male diagnosed with a chest wall sarcoma. After the surgical team made the decision to remove the sternum and a portion of the rib cage, they searched for a sternal reconstruction implant that would not only guarantee preservation of respiratory mechanics, but also provide adequate mediastinal protection and acceptable cosmetic results. To do so, they approached Anatomics (Melbourne, Australia).
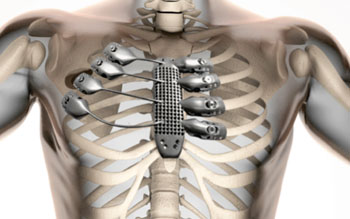
Image: The 3D printed titanium sternum and ribs (Photo courtesy of CSIRO).
Using high resolution computerized tomography (CT) data, Anatomics was able to create a 3-D reconstruction of the chest wall and tumor, allowing the surgeons to plan and accurately define resection margins. They then manufactured the reconstruction implant out of surgical grade titanium alloy using laser sintering printing techniques at the Australian Commonwealth Scientific and Industrial Research Organization (CSIRO, Melbourne, Australia) 3-D printing facility, known as Lab 22.
The 3-D printed implant that was fabricated consists of a rigid sternal core and semi-flexible titanium rods that act as prosthetic ribs attached to the sternum. During the resection, the surgeons used an intraoperative template to set resection margins so that the implant could be precisely placed. They also used a new and safer rib fixation system to connect the implant to the remaining sections of the ribcage. The design methodology and surgical procedure were described in a study published on August 4, 2015, in the European Journal of Cardio-Thoracic Surgery.
“We thought maybe we could create a new type of implant that we could fully customize to replicate the intricate structures of the sternum and ribs. We wanted to provide a safer option for our patient, and improve their recovery post-surgery,” said lead surgeon José Aranda, MD. “The operation was very successful; thanks to 3-D printing technology and a unique resection template, we were able to create a body part that was fully customized and fitted like a glove.”
“We wanted to 3-D print the implant from titanium because of its complex geometry and design. While titanium implants have previously been used in chest surgery, designs have not considered the issues surrounding long term fixation,” said Andrew Batty, CEO of Anatomics. “Flat and plate implants rely on screws for rigid fixation that may come loose over time. This can increase the risk of complications and the possibility of reoperation.”
“We built the implant using our AUD 1.3 million Arcam printer. The printer works by directing an electron beam at a bed of titanium powder in order to melt it. This process is then repeated, building the product up layer-by-layer until you have a complete implant,” concluded Alex Kingsbury, of the CSIRO manufacturing team. “3D printing has significant advantages over traditional manufacturing methods, particularly for biomedical applications. As well as being customizable, it also allows for rapid prototyping, which can make a big difference if a patient is waiting for surgery.”
Related Links:
Salamanca University Hospital
Anatomics
Australian Commonwealth Scientific and Industrial Research Organization (CSIRO)