Biodegradable Implants Result in Fewer Surgeries
By HospiMedica International staff writers
Posted on 19 Nov 2014
Load bearing, biodegradable implants made from iron-tricalcium phosphate (FE-TCP) degrade completely in the body. Posted on 19 Nov 2014
Researchers at the Fraunhofer Institute for Manufacturing Technology and Advanced Materials (IFAM; Bremen, Germany) and other Fraunhofer Institutes participating in the DegraLast project joined forces to design degradable bone implants for use in trauma surgery and orthopedics. A principal requirement for the suitable material included a degree of degradation matched to bone growth, so that the resorption of the implant meshed with bone formation. The implants also had to be mechanically stable enough during the entire healing process, and could not have any allergenic effects or cause inflammation.
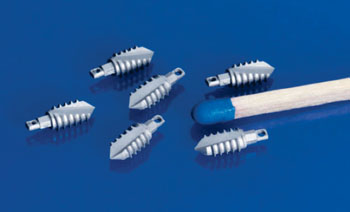
Image: Demonstrator suture anchors made of FE-TCP (Photo courtesy of Fraunhofer IFAM).
The researchers decided that a metal-ceramic composite would be a suitable candidate, but found that a key component in the design was to determine the right amount of ceramic as a function of the powder amount, since if the proportion is too high, the material would be brittle and accelerate the degradation of the implant. The final powder composition had a 60% iron alloy component and a 40% beta-tricalcium phosphate (TCP) ceramic component. Finally, they fabricated a biodegradable shoulder suture anchor using a powder injection molding technique.
While shaping processes such as powder injection molding are especially suited in large quantities as fixation elements for standard implants, additive manufacturing methods are often used to produce individual, custom-made implants—such as for bone replacement in the skull area—or implants with defined pore structure. The researchers are thus also testing implants made of magnesium alloys through the use of selective laser melting (SLM). The researchers presented the demonstration anchor at the COMPAMED trade fair, held during November 2014 in Düsseldorf (Germany).
“Iron alloys corrode slowly and ensure high mechanical strength, while ceramic decomposes quickly, stimulates bone growth and aids the ingrowth of the implant,” explained Philipp Imgrund, PhD, manager of the Medical Technology and Life Sciences business field at IFAM. “The degradation rate of the anchor of 240 micrometers per year means that the shoulder anchor would be absorbed by the body completely within one to two years.”
Related Links:
Fraunhofer Institute for Manufacturing Technology and Advanced Materials